Aiming at the shortcomings of traditional humanoid robots in real-time control and visual recognition of control system, S3C6410 is used as the main control chip. The humanoid robot control system with visual recognition function is designed. Good target recognition is achieved by improving and simplifying the video recognition algorithm. effect. Experiments show that the humanoid robot designed based on the control system has good real-time performance, accurate target recognition, and can quickly find the target by adjusting the motion path.
Intelligent mobile robot is a comprehensive discipline developed in recent years, involving mechanical design, sensing, artificial intelligence and many other aspects. The humanoid robot's control system is divided into three levels: the top layer is the robot's strategic planning layer, which uses various algorithms to implement the functions of each part; the middle layer runs the embedded real-time operating system of various applications; the bottom layer is the hardware. The platform obtains various types of data and information through the peripheral interface.
The autonomous robot uses the information acquired by the sensor to control the motion of the robot. According to the actual needs of martial arts robots, this paper designs the control system of the robot to realize the functions of camera image acquisition, processing and steering control.
In the strategy planning layer, because the image information has rich information and complete description of the scene, the color target positioning is mainly realized by processing the image information collected by the camera. Here, the Linux embedded operating system is adopted. Due to the limitation of the embedded system resources, the target recognition algorithm is required to operate efficiently and occupy a small memory space. The hardware platform mainly controls the steering gear to realize the motion control of the robot.
1 system control circuit and video recognition algorithm
1.1 Overall architecture of the robot
In the martial arts technical challenge, the robot collects the position information of the target. Due to the limited effective detection distance of I/O and A/D conversion, the robot uses the camera to collect image information on the site, and recognizes and locates according to the color of the target. When the target position is detected, the autonomous movement of the steering gear is controlled to move closer to the target, and the self-introduction and the hydrangea are completed. The designed robot is shown in Figure 1.
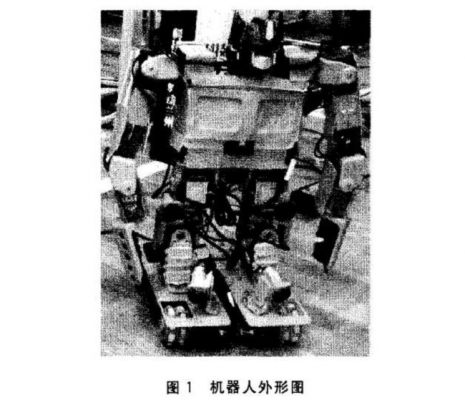
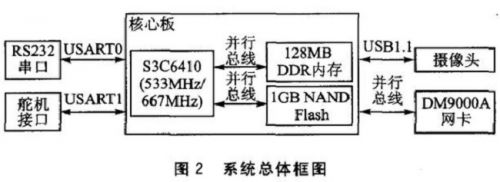
As can be seen from the figure, the robot head is connected to the main control board through a USB interface for capturing image information. The joints of the waist, legs and arms of the robot have a certain degree of freedom by using the steering gear. The steering gear used is the CDS series digital steering gear. It has an ATmega8 chip inside, and the main control board communicates with ATmega8 through the serial port, which can realize the control of the servo. In response to the above requirements, and considering the real-time nature of the system, S3C6410 is used as the main control chip. The overall block diagram of the actual control system is shown in Figure 2.
1.2 Steering gear control system design
The main control board completes the data communication with the servo through the serial port 1. The schematic diagram of the servo control circuit is shown in Figure 3.
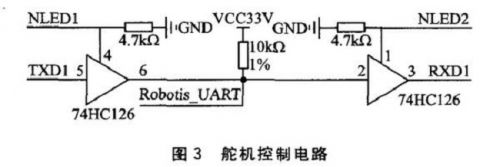
Since there is only one half-duplex data line, the separation between transmission and reception must be implemented on the circuit. Here, the network Robotis_UART is directly connected to the signal line of the servo, and the other end of the 74HC126 is connected to the TXD1 and RXD1 of the main control chip respectively, and then the main control chip is enabled to determine whether to send or receive. data. The main control chip can make NLED1 high and NLED2 low. At this time, TXD1 gains control of the line, and the main control chip can send data to the servo. Conversely, when NLED2 is high and NLED1 is low, then RXD1 takes control of the line, and the servo can return data.
For the software of the servo control, the configuration of the serial port needs to be completed, including the baud rate, the starting digit, the number of data bits, the number of stops, and the flow control mode. It is configured here to have a baud rate of 19,200, a start bit of 1 bit, a data bit of 8 bits, a stop bit of 1 bit, and no flow control mode. The setting of the serial port is mainly to set the member values ​​of the struct termios structure, as shown below:
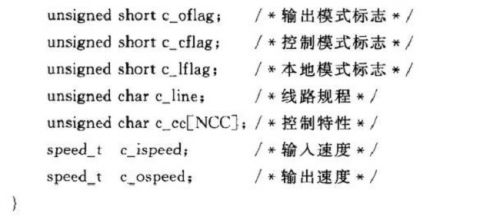
2 image recognition algorithm
The image captured by the camera is mainly processed as follows: firstly, the data is decoded, and the RGB spatial model data is converted into an HSI space model by using the look-up table method, and then the image is binarized by the inter-class variance method, and then the connected domain is used to perform the target. Calibration, and finally denoising the image to achieve target recognition and positioning. The image processing program flow chart is shown in Figure 4.
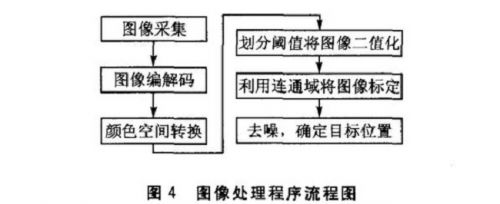
The images captured by the camera are in RGB format, but the R, G, and B values ​​in the RGB model are susceptible to light and are not suitable for color recognition. In the HSI model, different colors correspond to different hue parameters H, and H is less affected by external illumination. Therefore, the HSI model is used to achieve color recognition. Therefore, through some algorithm, the RGB gamut space is first mapped to the HSI space. The commonly used color space conversion algorithms are as follows:
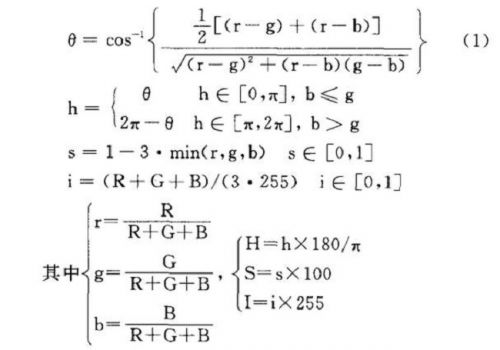


Thermal Relay is used to protect AC three-phase asynchronous motor/electric motor against overload and open phase. Korlen electrical appliances produce thermal relay switch in wholesale,being a good thermal overload relay suppliers from china. We also offers Manual Motor Startor , AC Contactor, led light, Circuit Breaker etc.
Thermal Relay,Latching Relay,Reed Relay,Polarized Relay
Wenzhou Korlen Electric Appliances Co., Ltd. , https://www.zjmannualmotorstarter.com